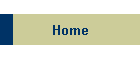
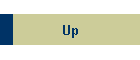
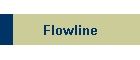
| |
WELDING FITTINGS |
BUTT-WELDING PROVIDES ADVANTAGES:
(Courtesy of FLOWLINE FITTINGS)
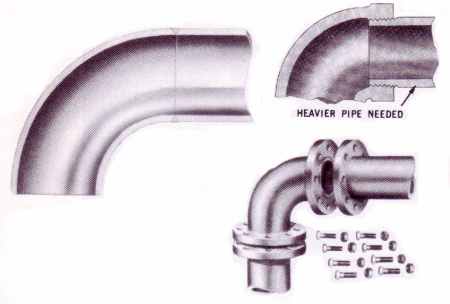
LOWER MATERIAL COSTS
A butt welding assembly uses less
material - a welded joint doesn't requrire extra wall for threading,
or extra material for flanging. |
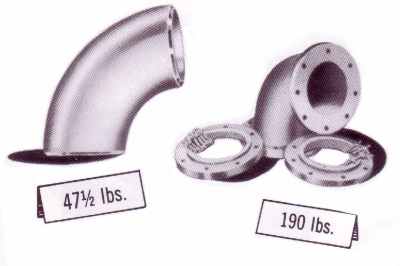
WEIGHT
A welded elbow connection weighs
approximately one-fourth as much as a flanged connection - an
extremely important consideration when multiplied by the number of
connections in a piping system. The excess weight serves no
useful purpose and places additional strain on the piping system. |
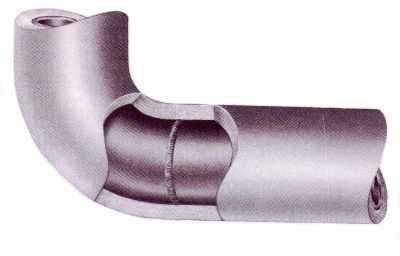
INSULATION
Piping joints can be insulated as
easily as the pipe and fittings. There are no protrusions to
complicate work. Finished system is streamlined and
economical. Leakproof - insulation lasts longer. |
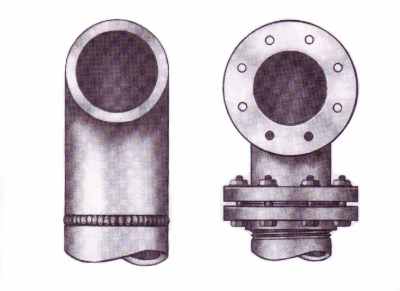
DESIGN
Welded construction permits the
greatest freedom in designing a layout. The system uses less
space: it is more compact, has greater strength. Can be installed
close to wall, ceiling, or floor. |
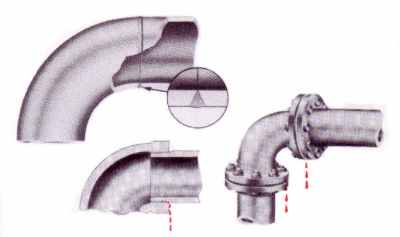
MAINTENANCE AND PLANT SAFETY
Permanently welded - significant to
savings in maintenance and repair costs. No problems with
threading, caulking, gasket replacement and bolt tightening.
Eliminates leaks potentially destructive to equipment and hazardous
to plant personnel. Proven dependability of forged material
for all components. |
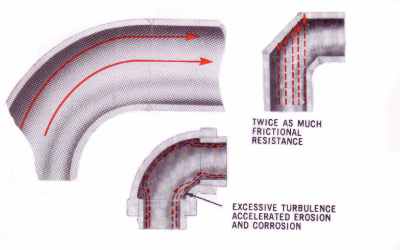
CLEAN...SMOOTH....FULL FLOW
A cleaner system with optimum flow
characteristics. No pockets or sharp corners to cause greater
frictional resistance, pressure loss, turbulence, erosion, and
product accumulation. |
|
|